www.industrymiddleeast.com
12
'14
Written on Modified on
Kollmorgen drives the lightweight helpers of Universal Robots
UR 5 and UR 10 are the names of the two models with which Universal Robots aim to establish the flexibility of articulated-arm robots in industrial production. The focus is on work areas in which conventional robots have thus far been too big, too expensive, and too loud. Due to their low weight they can be used wherever they are needed. A large part of the power density of the six-axis articulated robots comes from specially adapted KBM direct drive motors from Kollmorgen. Universal Robots was able to embed the motors directly into the articulation axes without need for additional housings.
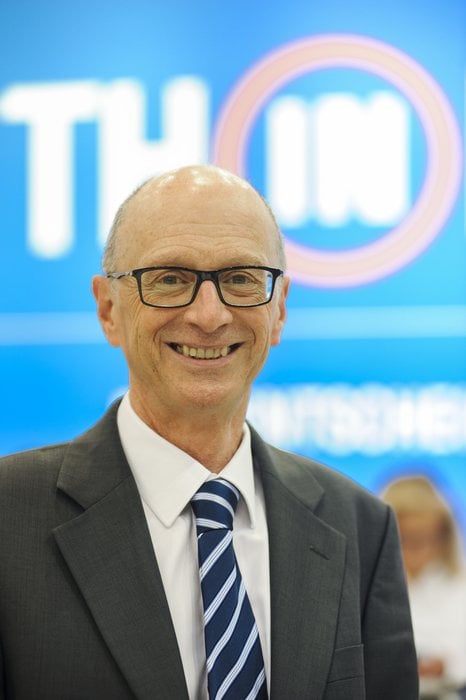
Author: Ian Young, Key Account Manager, Kollmorgen, Ratingen
Universal Robots (www.universal-robots.com) developed the UR5 and UR10 models for small and medium-sized enterprises in particular. The handling units lift a payload of five and ten kilograms, but only weigh 18 and 25 kilograms themselves respectively. This low weight makes it possible to move the units easily without complex subcomponents. The multi-functional robots are just as flexible in operation given their user-friendly software. This multi functionality supports the Danish company with a user-friendly piece of software. Using this, the six-axis lightweight robots are ready for new tasks in no time. No special knowledge of robotics is necessary for the programming.
Modular Design
The exceptional ratio of dead weight to loading capacity is the result of a sophisticated lightweight construction that does not contain anything it does not need. With the drive technology, this minimalist strategy means integrating Kollmorgen's frameless kit motors directly into the articulation axes. In so doing the robot takes on the function of the motor housing, while the gear unit simultaneously serves as the primary bearing of the rotor. Viewed as a whole, the components used by UR frequently take on multiple functions, and this ultimately reduces the number of mechanical components such as ball bearings, couplings, or shafts considerably, thus decreasing overall system weight and form factor. In addition, with their high power density, the Kollmorgen motors increase the lifting capacity of the UR5 and UR10 platforms. With their high power density, the KBM motors increase the lifting capacity of the UR 5 and UR 10 at the same time.
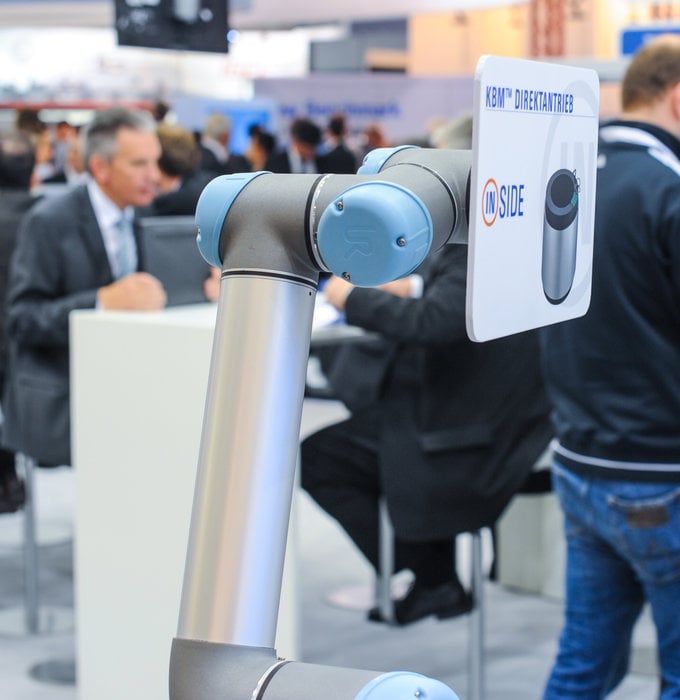
The six-axis robots are being used in processing and production facilities for example. The robots are easily programmed to accomplish repetitive tasks. Photo: Universal Robots
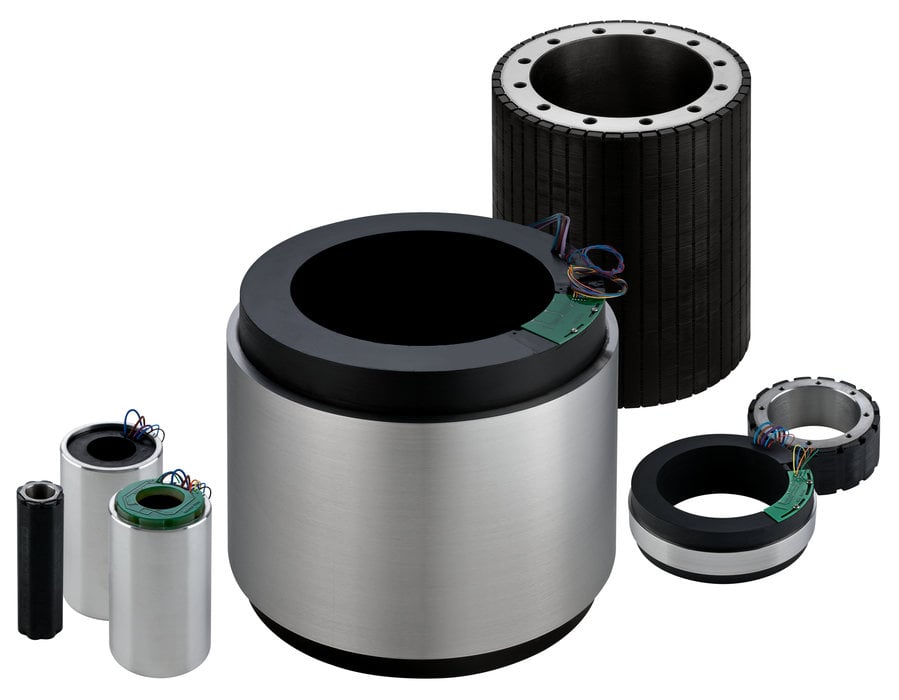
The KBM motors offer a great deal of freedom to configure the servo axes in a space-optimized way due to their variable, modular design. Photo: Kollmorgen
The KBM motor series offers advanced electromagnetic designs for optimized torque and minimal cogging and harmonic distortion. These benefits are offered over a large operating speed range. The electromagnetic technology with a high packing density in the stator increases torque and keeps thermal losses low. High strength rare earth magnets are used in the rotor, which allow a continuous torque of 1.45 to 3.445 newton meters along with a peak torque of 4.91 to 12.812 newton meters. "The high quality of these motors was a reason why we opted for Kollmorgen," explains Esben H. Östergaard, technical business manager of Universal Robots.
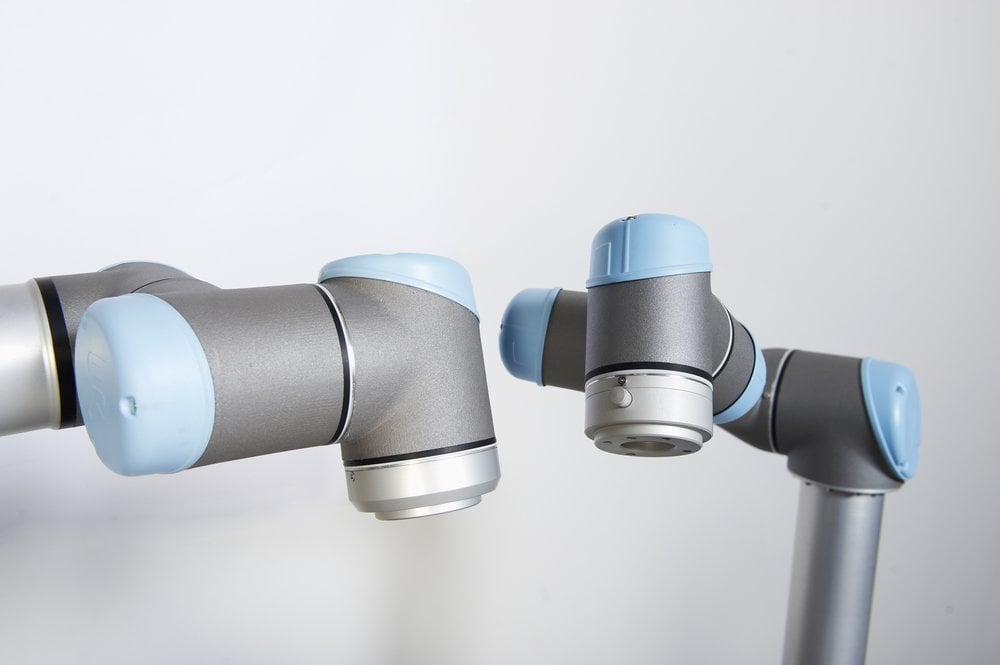
The UR 5 and UR 10 designs use KBM motors from Kollmorgen. They are integrated directly into the axis joint without a housing. Photo: Universal Robots
Given that the KBM motors are embedded in the robot housing and directly drive the load, the robots are able to achieve high level of precision in movement and force control. Targeted force control is critical in this regard, because the robots constantly have to move different workpieces perfectly with high variability. In practice they recognize the size and elasticity of the objects and adjust the force to be applied accordingly. This force must be stronger than just 25 newtons to do this. With a precision of ± 10 newtons and an accuracy of ± 5 millimeters, the required force and desired position can be programmed and executed for each of the six joints.
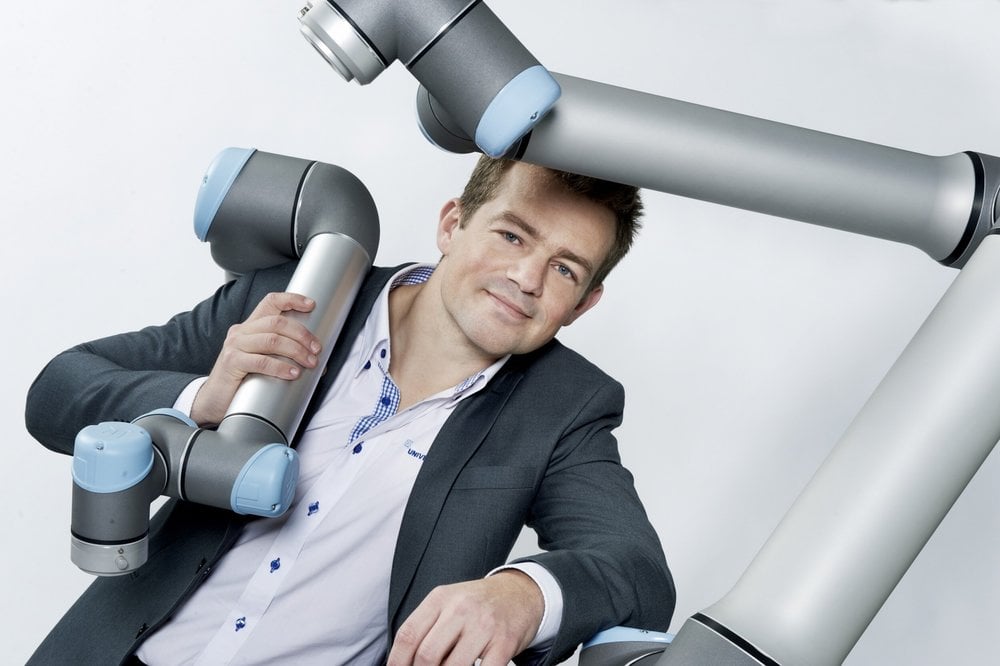
Esben H. Östergaard, technical business manager of Universal Robots, values Kollmorgen's high availability of supply in a constantly growing market. Photo: Universal Robots
Operation without noise but high energy efficiency
Another advantage of the robots is its low-noise and energy-saving operation. From a total-cost-of-ownership perspective, the economical use of resources directly increases the efficiency of the robots overall. The competitiveness of this technology thus increases as a result. An additional benefit of high energy efficiency is closely linked to reduced losses in the motors. As efficiency is high, less heat is produced. This means the motors stay cooler, operate below their maximum ratings, and consequently achieve a longer service life. The improved temperature behavior also prevents the entire construction from heating up. "The motors we used in the past became pretty hot when in continuous operation. Because of the lower losses, the KBM motors from Kollmorgen simply stay colder. We can therefore run our robots in continuous operation without derating," states Östergaard, and he refers to test procedures with long operation periods and comparatively high loads.
The KBM series is an innovative direct drive frameless motor technology provided by Kollmorgen. The frameless kit motors offer mechanical and plant engineering a wide range of solutions for creating applications with a maximum degree of flexibility, power density, dynamics, and durability. In addition to the technical advantages provided by this product, the KBM platform includes 14 frame designs and many pre-engineered standard options with competitive lead times. "We can basically order as many motors as we want, when and how we want," emphasizes Östergaard. This aspect is of particular importance because Universal Robots is growing strongly. "We therefore need a partner in drive technology who is a good fit for us." In this regard, Kollmorgen was able to impress the Danish robot specialists with delivery reliability and has since established a UR-specific production line at the Czech location in Brno.
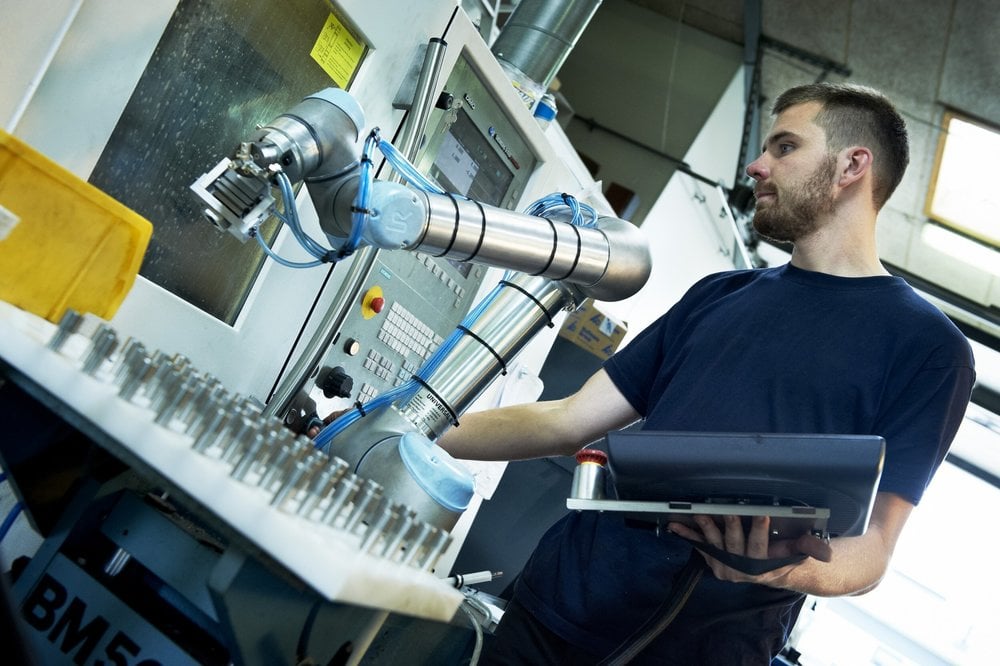
Close partnership with people: the robots from Denmark have been designed for collaborative work in production. Photo: Kollmorgen
KBM direct drive motors:
http://www.kollmorgen.com/en-gb/products/motors/direct-drive/kbm-series-frameless/
Prospects
Ultimately, the quiet operation and high-quality control of the synchronous servo motors ensure the robots can be used outside of handling applications, too. Up until now Universal Robots' focus has been to use the robots as a tool for performing simple tasks. "We are therefore not competing directly with other robot manufacturers who deal with more complex tasks. Instead we are saving people from having to perform tiring, monotonous manual work," stresses Östergaard. As the company from Odense has developed light constructions without uncontrollable oscillations and vibrations, however, there are new application possibilities; such as with welding and gluing. "We can expand our business channels," says Östergaard. This development is accompanied by the fact that due to sophisticated safety technology both models are even able to be employed without additional shielding. This opens the path to a safe and comfortable cooperation between staff and technology.